
Today, we are 70% done with 2016. Time flies, and some weeks it’s hard to notice any progress. The USAXS project, however, has been plodding along at a slow but steady pace. With the arrival of more machined parts, we are yet one more step closer to completion. Here’s how close we are:

As you will remember from the previous post, the instrument consists of Two Towers with the channel-cut crystals on top. In the middle, there is a platform for mounting a sample or sample stages (Figure 1). The two crystals are to be rotated very carefully in the incoming X-ray beam, and need a few alignment rotations as well. Since everything is supposed to be in a synchrotron hutch, everything is motorized for remote control.

The two crystals are enveloped in aluminium boxes (which I talked about last week). These will hopefully shield any unwanted odd reflections, which can emerge at odd angles and increase the background counts, while providing some safety for the fragile crystals as well. The position of the crystals along the box length can be fine-tuned using set screws. The crystals have been cut using opposing geometry, so that the beam translation in an instrument with and without this USAXS component will be minimized.
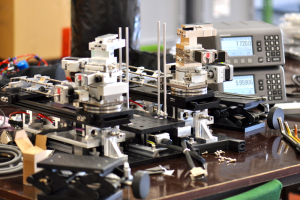
The fine rotations have this time been augmented with encoders at the end of the actuation arms (Figure 3). These will provide additional position feedback, and are apparently quite accurate. Whether movement of the arm end is identical to rotation is something which we can very easily see once the instrument is in an X-ray beam: note that we are going for sub-micro-radian rotation accuracy, so the reflection of the beam through the crystal will tell us whether we have designed correctlt. So far, the rotations appear to run very smoothly, courtesy of the high-precision cross-roller bearings, and the rod-based arm construction appears to be sufficiently stiff.
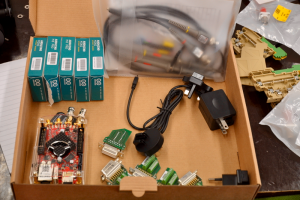
The instrument is controlled using pneumatic valves and stepper motor controllers, and the next step is, therefore, to integrate everything. For this, we are intending to use a Raspberry Pi 3 and some Arduino’s (Figure 4). For troubleshooting, we have a Red Pitaya and some probes standing by. Whether or not these will be used in the synchrotron as well remains to be seen. However, they have proven to be quite useful in other projects in the past, in particular where we converted an Arduino into a counter and ratemeter (we could probably have pushed that one much further). The electronics will undoubtedly be discussed at a later stage.
I hope you like the progress so far. I can’t wait to test the thing on an actual X-ray source!
Leave a Reply