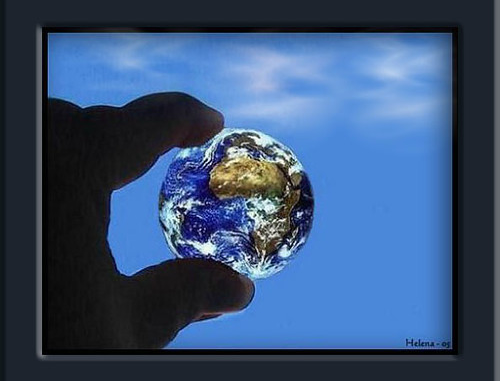
The blog post on standardized bases a few weeks ago led to a canSAS e-mail discussion, with everyone chipping in with their favorite bases. Here’s a brief summary of the findings from that discussion:

S-sized bases: The main options for small bases, with the beam approximately around 100 mm mount-to-beam distance, and a load capacity up to one to two kg are standard kinematic bases from Thorlabs and Newport. Quoting Adrian Rennie (AR): “it is sometimes tempting to design one’s own kinematic mounts to allow for a number of improvements for a particular application, but the real cost of manufacturing a small series is quite large. Particularly if they are to be adopted by many people, it is helpful to use parts that can be purchased readily”.
The Thorlabs KB75/M version costs about 90 Euros, and has a set of magnets in the base to hold the plates together. The advantage is that this could hold racks that can be placed by robotic arms. On the downside, if you have a small sample chamber with electric or liquid feeds, the feeds need to be led to the base of the plate before leading them off, as any sideways force high above may lead to the plate disengaging from the base. This base is in use in our lab, as well as at ISIS, ILL, and at Uppsala University, according to AR.
The other option is the Newport BKL-4, which comes in at 250 Euros, and is in use at the APS and the SSRL, with a 152 mm distance to the sample. The advantage of these is that they have a locking screw instead of magnets, introducing no stray magnetic fields onto the sample position, and not suffering from the same sensitivity to off-center loads as the Thorlabs ones. These would not be able to be placed robotically, however. Also, as Malcolm Guthrie (MG) at the ESS says “I have a lot of experience with that one, and it will give ±20 µm for small loads under 1 kg, but loses [accuracy] above 2-3 kg”.
The ESS is exploring alternative options including solutions such as those from Kipp designed for holding machine tables and work holding equipment. This may not be cheap, and may not have a rotation index. The ESS is designing their smallest level sample holder bases around the idea that they should be 200 mm from the beam, and can carry up to 10 kg with an interface area of about 250mm in diameter. That does make it approach our M-sized solutions..
For the M-sized solution, we have ours (and I22’s), with an approximately 300 mm distance between the base and the beam center, and an expected load of about 10 kg. The ESS goes one step further there, assuming a more cylindrical geometry of sample holders, with a distance to beam of about 350 mm, a maximum weight of 300 kg, and an interface area diameter of about 500 mm (adding a weight like that to our instrument might get us close to the maximum floor load limits of our laboratory…). The ESS is planning to forego ball-and-groove for this due to the high load on the contact points, but instead is thinking of choosing canoe-spheres due to their higher load capacity.
Beyond this, only the ESS has provided information on bigger levels. Their one-level-up has a distance of 500mm to the beam, a maximum weight of 1 ton, and an interface area diameter of about 800 mm. For floor-mounted equipment, they envision a distance to the beam of 1300 mm, a weight of 2 tons, and an interface area of either 1200×800 mm, or 850 mm diameter. That would mean that I could put the MAUS on a pair of their largest feet!
Leave a Reply